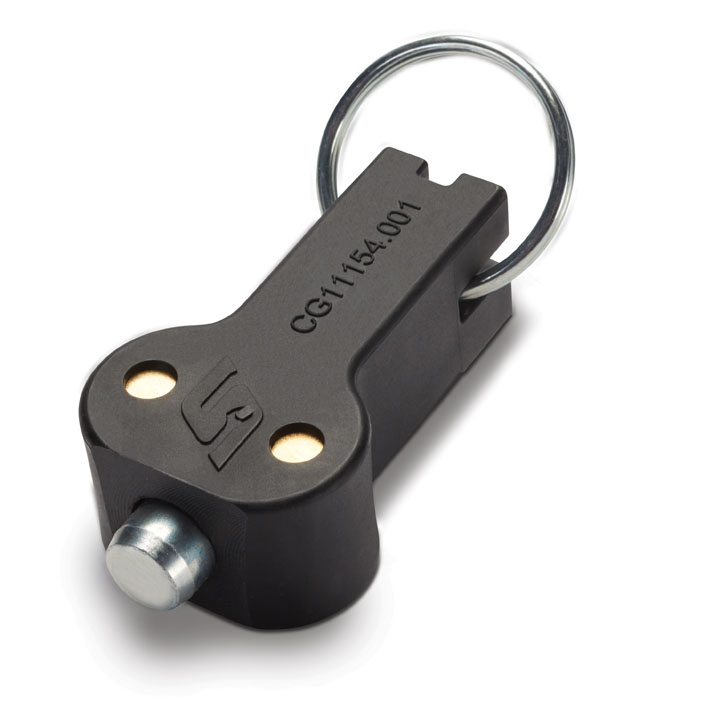
INSERT MOLDING
In this process, a metal substrate is placed into a mold cavity and encapsulated with plastic, resulting in:
- Faster assembly time
- Cost effective solutions
Colson Group has over 20 years of experience with standard horizontal injection molding machines.
OVERMOLDING
In this process, the base layer is molded first and the additional plastic layer(s) are molded over and around the original part, resulting in:
- A single finished product for added strength
- Long service life
- Enhanced safety
OVERMOLDING
In this process, the base layer is molded first and the additional plastic layer(s) are molded over and around the original part, resulting in:
- A single finished product for added strength
- Long service life
- Enhanced safety
THICK-WALLED AND
COMPLEX PARTS
We specialize in thick-walled, large-shot molding with the additional ability to handle difficult, complex shapes.
Let us help you design and develop a new product, or help solve current product design problems.
MATERIAL EXPERTISE
Partnerships with major material suppliers give us the ability to develop and test custom high-quality, low-cost materials that are certifiable and provide constant traceability for your unique application. Materials processed include, but are not limited to:
- High-temperature materials
- Acetal
- Nylon 6
- Polyurethanes
- Thermoplastic Elastomers (TPE/TPR)
- Polyethylene
- Polypropylene
- ABS
- Polyesters
- Polyvinyl Chloride (PVC)
- Polycarbonate
- Glass-filled materials
- Thermoplastics
MOLD DESIGN & BUILDING
Our team of designers, engineers, and technicians can help develop and build your mold with quality testing at one of our state-of-the-art Colson Group facilities.
Upon completion, the engineering team prepares the mold for tryout and works with the Colson Group quality team to ensure part dimension validation and visual acceptance.